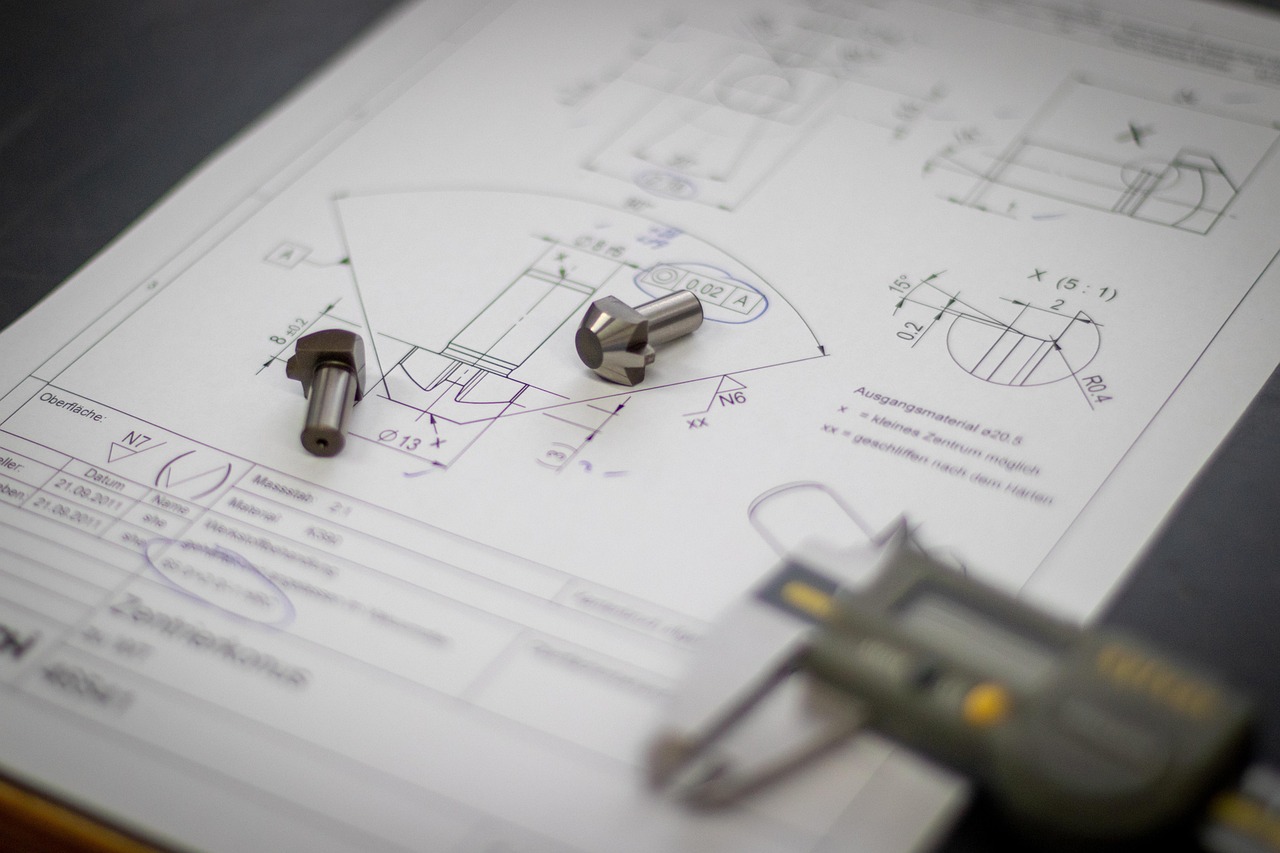
From raw materials being delivered to the assembly line, to finished products waiting to be shipped, every step of production requires precise tracking. Without visibility, inefficiencies and mistakes can quickly spiral out of control. This is where RFID in manufacturing comes in, transforming how manufacturers keep tabs on their operations.
Imagine a scenario: A worker needs to locate a specific part to complete an assembly. Without RFID, the process involves searching through piles of materials or relying on outdated spreadsheets. Time is lost, and the risk of errors increases. But with RFID technology, that same worker can instantly scan the part and find its exact location – whether it’s on the production floor, in storage, or in transit. RFID enables real – time tracking, offering a level of visibility that can revolutionize how a manufacturing plant operates.
Real – Time Data for Smarter Decisions
RFID systems provide real – time data on materials, equipment, and products as they move through the production floor. Instead of relying on manual counts or periodic inventory checks, manufacturers can track every item as it enters, moves through, and exits each stage of production. This immediate access to data ensures that workers, managers, and supervisors have up – to – date information, helping them make better decisions faster.
In fact, recent studies show that manufacturers who adopt RFID technology see a significant boost in their operational efficiency. According to a 2023 report by the Manufacturing Technology Insights magazine, 72% of manufacturers in the UAE have reported improvements in production floor visibility and operational efficiency after implementing RFID solutions. This technology helps manufacturers stay ahead of potential issues, reduce delays, and maintain a smooth flow of production.
Reducing Downtime with RFID
For many manufacturers, unplanned downtime is one of the biggest productivity killers. Whether it’s a machine that’s overdue for maintenance or missing inventory causing delays in production, downtime can halt everything. RFID technology minimizes this risk by allowing managers to track the status of both equipment and materials in real time.
By placing RFID tags on machinery, manufacturers can monitor usage patterns and condition. This data can then be used to predict when maintenance is needed, preventing breakdowns before they occur. For example, a manufacturer in the UAE reported a 30% reduction in unplanned downtime after integrating RFID – based predictive maintenance into their operations.
Improved Inventory Accuracy
Inventory discrepancies are a common challenge on the production floor. Misplaced parts, stockouts, or overstocking can disrupt manufacturing schedules and lead to costly delays. RFID offers a straightforward solution. Each item in the inventory is tagged and can be scanned quickly and accurately, providing a real – time update on stock levels and locations.
The ability to track parts and materials in real time means that manufacturers can eliminate stockouts, prevent overstocking, and optimize their entire supply chain. A survey by IDC Manufacturing Insights found that RFID in manufacturing helped reduce inventory errors by over 40% in plants across the UAE, making it a crucial tool for maintaining accuracy on the floor.
Fostering a Smarter, More Efficient Manufacturing Environment
With the integration of RFID, manufacturers aren’t just improving visibility – they’re enhancing their entire operation. The ability to track materials, monitor equipment, and gain real – time insights leads to smarter decision – making, faster response times, and a more efficient production process overall.In the UAE and around the world, more manufacturing plants are adopting RFID solutions to take control of their operations and reduce errors. By bringing transparency to every stage of production, RFID helps manufacturers build smarter, more agile plants that can respond quickly to challenges, keep costs low, and maintain a high standard of quality.